DUGAA® provides enterprise-grade product-component management systems for global manufacturers. We help companies collaborate across departments for accurate product specification data, also with the worldwide repair sites to handle the intricacies of after-sales management: repair workflows, complex warranty, return-to-vendor, safety stock material prediction and planning, Last-Time-Buy service parts forecasting, component phaseout demand predictions, and other critical operations.
By using DUGAA solutions, we connect multi-dimension data relations and bring visibility not just at the product level, but details up to the component level.
The manufacturing industry nowadays needs to have the ability to produce lower quantities of more variety of products to meet new market demands. The agility of manufacturing also brings complexity to the after-sales repair services.
Manufacturers need to provide stable, long-term and high-quality after-sales service to gain the trust of B2B customers and enhance their competitiveness.
Most of the current enterprise software focuses on manufacturing, finance, customer relationship, sales and marketing.
Typical enterprise software cannot handle the intricacies of after-sales repair workflows, complex warranty, return-to-vendor, safety stock material planning, Last-Time-Buy service parts forecasting, component phaseout demand predictions and other critical operations.
For global manufacturers, problems get more complicated when data cannot be synchronized, global staff cannot collaborate, or interact with customers in real time. These may delay the company's growth and expansion.
With war, pandemics, climate crisis, shortage of REE, component shortage, regulations, tariffs and global supply chain disruptions.
Manufacturers need advanced solutions to tackle emerging challenges in the fast-changing world. DUGAA solutions are built to help manufacturers to be well-prepared and turn the crisis to opportunities.
ERP (Enterprise Resource Planning) systems are primarily designed to manage and integrate various business processes, such as finance, human resources, inventory, and procurement.
After-sales repair management, on the other hand, involve managing the return or replacement of products due to defects or damage, customer interactions, multi-level warranty checking, component-level analysis, and even advanced safety stock material planning for the unpredicted repair services.
While ERP systems can play a role in supporting certain aspects of after-sales return services, the unique requirements and complexities of product returns and AI predictions often necessitate dedicated management systems or specialized software solutions.
Manufacturers need to provide stable, long-term and high-quality after-sales service to gain the trust of B2B customers and enhance their competitiveness.
The after-sales service department plays an important role. They have heavy workloads but lack proper systems. Mostly the work is done manually or with primitive methods which are time-consuming and labor-intensive.
XMRP® is built and equipped with our proprietary machine learning technologies to tackle unknowns and uncertainties of after-sales material planning, providing predictions for manufacturers to prepare and forecast the after-sales product repair materials.
RMAONE® is a global Return Merchandise Authorization(RMA) management system, which is built for manufacturers to manage their global RMA with worldwide B2B clients.

We use big data and AI to process large amounts of product and component data. The system runs through multi-layers of data quality checks to verify whether the data and its relations are logically correct. High-resolution data and high-quality data are crucial in helping your staff get correct data in real-time, improving the precision of data analysis and predictions.

Compared with typical enterprise software, which usually has a 2D rows and columns view of the data, in DUGAA systems, we rapidly connect the incoming data and generate multi-dimension data relations, uncovering hidden insights and data analysis that manufacturers might never see before.

At DUGAA, we help global manufacturers collaborate with their worldwide branches, repair sites, B2B clients and vendors. The administrators in the headquarters can create users accordingly, allocating zones and functionalities that are absolutely required for each user to perform routine and legitimate activities, improving security and enhancing each user’s learning curve.
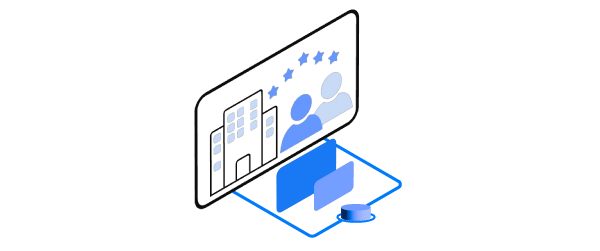
Users in every branch can get their after-sales information accordingly, such as RMA submitted by their regional customers, warranty information, safety stock machine learning predictions, as well as check the material excess quantity in other repair sites, to make sure that all repair centers can deal with their after-sales management swiftly and accurately and answer customers' demand on time.